A couple of months back, a team working at the Wyss Institute at Harvard developed an engineering solution—SWIFT—that endeavored to make 3D-printed organs more viable. With it, the researchers were able to create a synthetic perfusable cardiac tissue that could beat synchronously for seven days. Now, there is another development in the domain of 3D printing by the same institute.
Researchers at the Wyss Institute have developed a technique that will apparently speed up the manufacturing of complex, 3D-printed objects significantly. To achieve this feat, the technique, dubbed multimaterial multinozzle 3D printing (MM3D), uses high-speed pressure valves to seamlessly switch between eight distinct printing materials to create complex shapes and objects. Each valve, according to the team, "is capable of switching materials at up to 50 times per second, which is faster than the eye can see, or about as fast as a hummingbird beats its wings."

Subsequently, this will speed up the printing process. And the team claims that MM3D will require only a fraction of the time used to create such objects with traditional methods that involve the use of single-nozzle and large multi-nozzle printheads.
Mark Skylar-Scott, one of the co-first authors of the paper, commented on the team's work, claiming that the technique transforms the relationship between the time required to print an object and its length from a cubic to a linear time complexity:
"MM3D’s combination of multinozzle arrays with the ability to switch between multiple inks rapidly effectively eliminates the time lost to switching printheads and helps get the scaling law down from cubic to linear, so you can print multimaterial, periodic 3D objects much more quickly."
The key element of the technique is the set of Y-shaped junctions that are precisely tuned to prevent mixing or backflow of the inks during printing. For printing large objects, these junctions can be multiplexed. Concretely, this rapid one-way, continuous stream of ink enables the precise construction of complex parts using reactive materials such as silicones, polyurethanes, epoxies, or bio-inks.
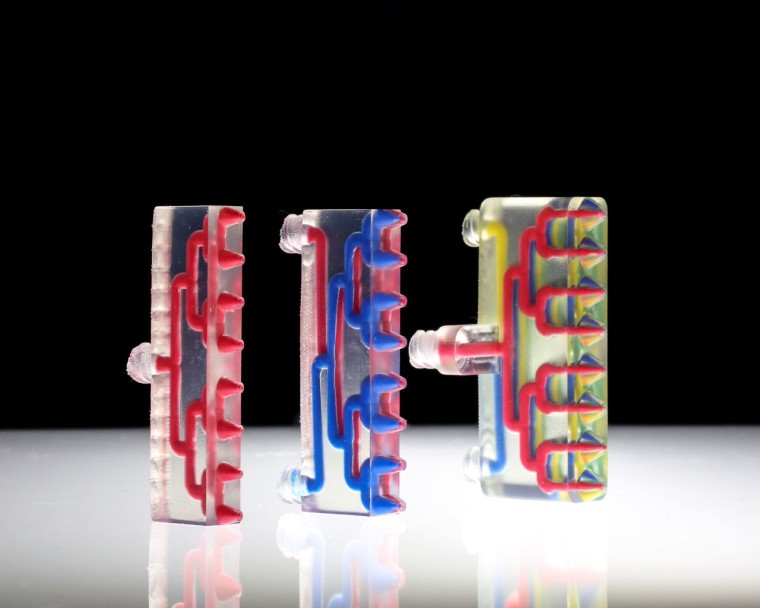
Skylar-Scott's team demonstrated MM3D by printing a "Miura origami structure composed of stiff 'panel' sections connected by highly flexible 'hinge' sections." Unlike traditional methods, which would have required considerable time and needed multiple layering, the "MM3D printhead was able to print the entire object in a single step by using eight nozzles to continuously extrude two alternating epoxy inks whose stiffnesses differed by four orders of magnitude after being cured."
The researchers also employed MM3D to print a walking "soft robot composed of rigid and soft elastomers in a millipede-like pattern." Impressively, "the robot was able to move at nearly half an inch per second while carrying a load eight times its own weight, and could be connected to other robots to carry heavier loads."
Currently, MM3D can only print periodic, patterned objects. But the team at Wyss believes that with further development and research, particularly in the use of sacrificial inks, will allow the process to create even more complex structures in a single step.
All in all, Donald Ingber, the Founding Director of Wyss, saw potential in the technique for the manufacturing industry, and remarked that "this new advance [MM3D] promises to dramatically improve the pace of innovation in this exciting area."
For more information, you may study the paper published on Nature.
4 Comments - Add comment