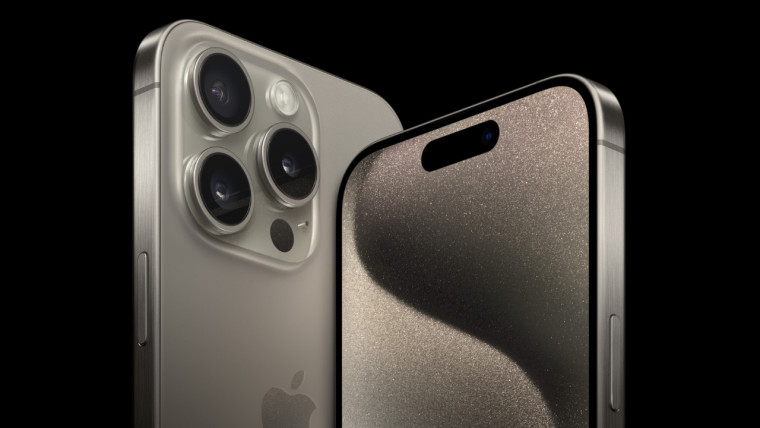
Apple's iPhone models come with water and dust resistance ratings as high as IP68 in the case of the latest iPhone series. But have you ever wondered how the Cupertino giant stress tests its devices to achieve the required durability and resistance against water ingress?
Tech reviewer Marques Brownlee shared a thread of posts on the social media platform X (formerly Twitter), giving an insider look at the kind of water testing methods and machines Apple houses under its roof.
Apple iPhones go through multiple levels of water testing to achieve different IP ratings. For instance, Level 1 (IPX4) involves simulating rain using a drip tray with no real pressure. Level 2 (IPX5) includes a sustained low-pressure jet spray.
In Level 3 (IPX6), a machine throws high-pressure water at the iPhone mounted in front of it. Finally, the iPhone is locked underwater and pressure is added to simulate depth for a long period to achieve IPX8 water resistance.
#2: There's an entire room of machines for water and ingress testing
— Marques Brownlee (@MKBHD) May 29, 2024
Level 1: A drip tray simulating rain, no real pressure. IPX4
Level 2: A sustained, low-pressure jet spray from any angle. IPX5
Level 3: High pressure spray from a literal firehose. IPX6
Level 4: Locking the… pic.twitter.com/5R38I6QVmW
Having a watertight device might take a toll on areas like repairability. Commenting on the balance between durability and repairability, Apple's Head of Engineering John Ternus said "you can actually do the math and figure out there is a threshold at which if I can make it this durable then it's better to have it a little bit harder to repair."
Ternus explained that water ingress was a common problem during the iPhone's early days, for instance, the device often failed if it was dropped in a pool or a drink spilled over it. The company has improved its devices over the years to minimize those failures.
"To get the product there, you gotta design a lot of seals, adhesives, other things to make it perform that way, which makes it a lot hard to do that battery repair," he added. "You still need to do the battery repair, so we need to make sure we have solutions for customers to do that, which we do."
Apple offers in-store battery replacement for a fee and has a Self Service Repair program that lets users with required knowledge replace device parts, including battery, display, and camera. While the company has been in hot waters over repairability, it has made things easier in recent years.
According to Ternus, it's "objectively better for the customer to have that reliability" and better for the planet because the failure rates have dropped. Even if the device is super repairable, "every time you're bringing in new materials, you know, to replace whatever broke."
#3: Apparently Apple has also bought and programmed and industrial robot to be their own drop test machine - to simulate hundreds of different drop angles onto different materials
— Marques Brownlee (@MKBHD) May 29, 2024
Then they hit it with some ultra bright lights and a high speed camera to watch them back in… pic.twitter.com/EsNJbVQrbO
Apple has been growing its suite of durability tests over the years and the company may test over 10,000 pre-release units of any given iPhone before the product gets shipped. Apart from water ingress, Apple has specialized hardware and robots to mimic the vibrations from motorcycle engines or simulate hundreds of different angles for drop tests.
1 Comment - Add comment